Nuevas tecnologías para la fabricación de estructuras de acero
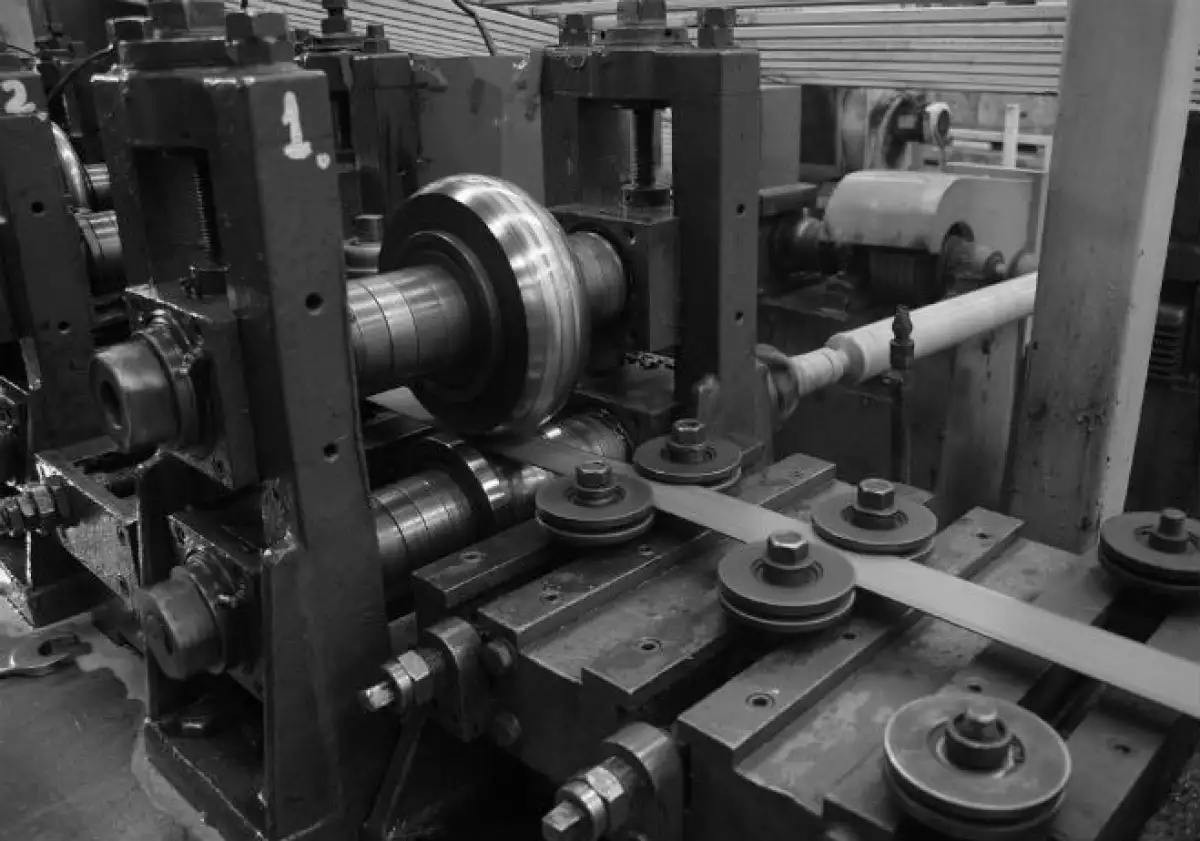
Por Carlos Cházaro Rosario*
*Director de operaciones CHC Ingenieros
La fabricación es el proceso de convertir materia prima en estructuras de acero y, en este sentido, se denomina materia prima a los perfiles laminados y placas de acero provenientes de un proceso siderúrgico. Es así que el costo de una estructura está compuesto por los materiales, la fabricación, el transporte y el montaje.
El objetivo de un taller de estructuras se debe concentrar en sacar producción en serie de elementos que sean iguales en un mismo proyecto; es decir, desde el diseño se debe prever que sea de rápida y fácil elaboración, pues está estrechamente relacionado con la maquinaria y equipos dispuestos en un taller.
Cuando un taller trabaja de manera arcaica, con mecanismos de trazo manual para el habilitado de las piezas, de corte con equipo mecánico y soldadoras manuales o semiautomáticas, la producción de estructuras será más lenta y con un alto porcentaje de errores durante todos los procesos.
De lo anterior, lo que no podemos dejar de lado es el gasto que representan los consumibles de la operación de dichos equipos. Lo más adecuado es que los talleres inviertan en dispositivos de control numérico capaces de aumentar la producción y obtengan ahorros importantes por el bajo costo de los consumibles.
Hoy en día, existen maquinarias y equipos de control numérico (CNC) capaces de aumentar hasta en 200% lo que se produce en un taller convencional. Además, estos aparatos se alimentan de información BIM, con lo que se obtienen ahorros de tiempo y disminución de errores.
El proceso contempla los siguientes pasos:
1. Recepción del material. Con los avances tecnológicos en paqueterías de desarrollo ingenieril y administrativo, desde la entrada de material, se puede desarrollar un sistema de control de inventarios, así como de las salidas de productos terminados, a tal grado de conocer a la persona que fue responsable de armar y de soldar una pieza.
2. Corte y habilitado. Se pueden presentar equipos de plasma para el corte de placa y perfiles, tales como los pantógrafos que se encargan, en la mayoría de los casos, de cortar todo lo relacionado con las conexiones en un proyecto. Igualmente, existen equipos de plasma que además de cortar, marcan las piezas e incluso pueden barrenarlas para la instalación de tornillos de alta resistencia.
3. Armado y soldado. Para que esta etapa de fabricación sea excelente, es indispensable que el armador pueda tener, perfectamente, la ubicación de todos los elementos que constituirán la pieza. El objetivo es que el soldador se despreocupe de la parte de la precisión en el armado y se dedique exclusivamente a soldaduras definitivas. Para esta parte del proceso se pueden mencionar equipos de arco sumergido en el caso de soldadura.
4. Marcado. Cuando se fabrica una pieza, se debe pensar en el siguiente proceso, es decir, el montaje de la estructura en campo. Para ello, la pieza deberá ir perfectamente identificada para que el ejecutor tenga claro donde colocar el elemento. En este caso, existen equipos capaces de marcar la pieza para su plena identificación.
5. Pintura. Es importante dar protección temporal o definitiva a la estructura y en este punto pueden emplearse equipos de pintura totalmente automatizados.
Sin duda, los talleres con maquinaria y equipo de ultima generación son una muestra de avance tecnológico, calidad en el producto y de rapidez en la ejecución. En términos generales, para que un taller de estructura sea óptimo deberá hacer más con menos.