¿Cómo seleccionar un 'escudo' para el equipo eléctrico?
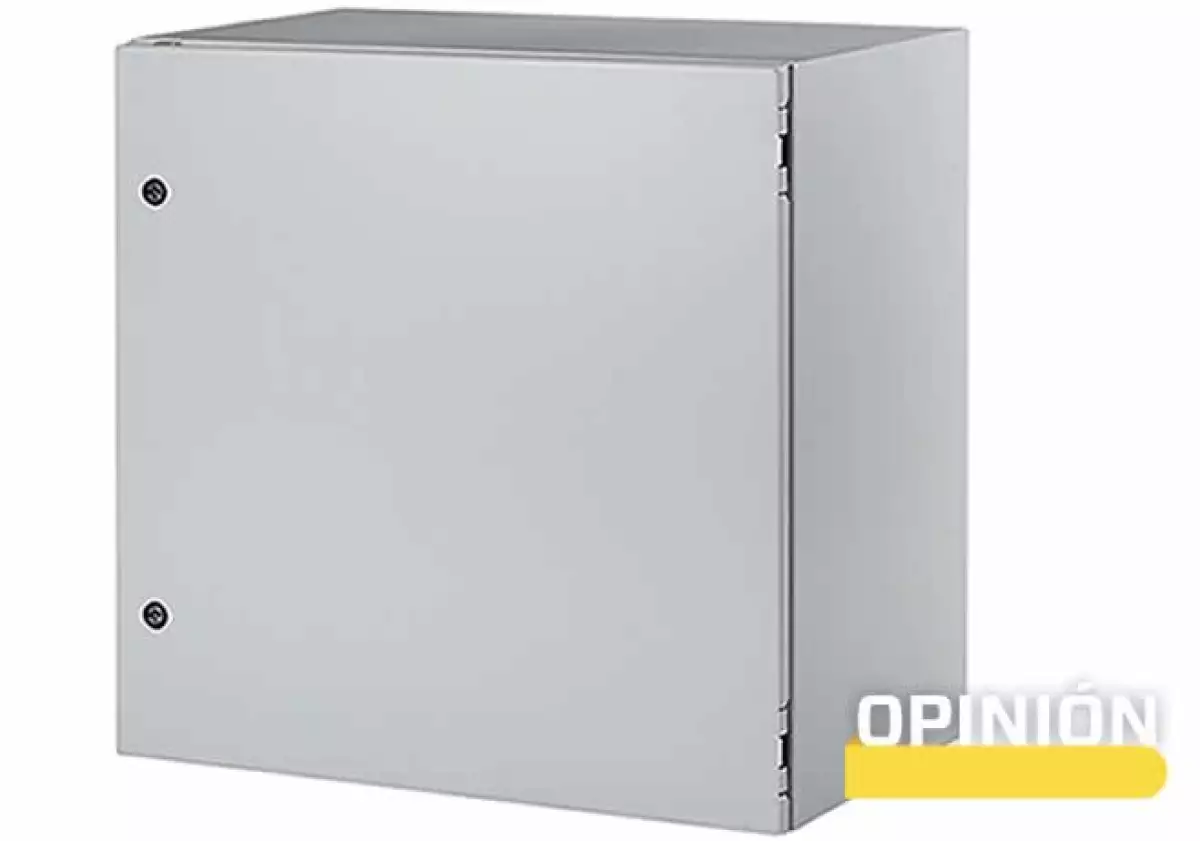
La protección de equipo eléctrico no es algo que debamos tomar a la ligera, hay que buscar alternativas que nos garanticen el correcto funcionamiento de los equipos. Es por ello indispensable que al momento de darnos a la tarea de seleccionar un gabinete tomemos en cuenta todos los detalles necesarios para que funcionen de manera óptima y uno de ellos tiene que ver con los empaques. Pero ¿por qué algo tan pequeños puede representar un riesgo? La respuesta es simple, para evitar que por los orificios destinados para la instalación entren elementos del medio ambiente –polvo, suciedad, agua o interferencia electromagnética- que afecten la operación de los equipos.
De hecho, los empaques son dispositivos mecánicos utilizados para proporcionar un sello hermético entre dos superficies de contacto articuladas, ligeramente irregulares, tales como el gabinete y sus puertas y accesorios. Su principal objetivo es evitar que entren contaminantes y fuentes de interferencia a un gabinete y, en algunos casos, que salgan ruidos de los mismos. Por lo tanto, debe ser diagnosticado adecuadamente para el ambiente en el que será utilizado, con el objetivo de garantizar un desempeño confiable.
Un modelo para cada necesidad
Cuando inicia la búsqueda es impresionante ver que actualmente existen diferentes modelos, tamaños y estilos, que hacen pensar en una decisión más complicada, pero no es así. La buena noticia es que la gran variedad se debe a que cada una de las opciones se adecua a cada necesidad, tomando en cuenta el lugar en dónde se va a utilizar, el medio ambiente, así como los materiales del gabinete.
De hecho, tenemos a la mano una clasificación general que nos ayuda en la búsqueda, la cual destaca tres principales tipos de empaques: en tiras, de espuma (FIP por sus siglas en inglés Foam In-Place) y cortados a la medida. ¿Pero en qué consiste cada uno de ellos?
Para el empaque en tiras —el método más antiguo y económico— los fabricantes adhieren rollos o tiras a la superficie del gabinete y las cortan a la medida. La desventaja es que produce una unión en cada esquina que puede hacer que el empaque sea más propenso al desgaste y, en consecuencia, al daño.
Por su parte, el FIP es el tipo de empaque más popular. En este normalmente se aplica al gabinete material de poliuretano de manera líquida y posteriormente se deja secar hasta formar una espuma celular en el cuerpo o la cubierta del gabinete. El proceso de formación no deja uniones. Esta alternativa ofrece una buena resistencia en la compresión de ajuste.
Mientras tanto, los empaques a la medida se encuentran disponibles en dos formas: empaques regulares a la medida y Chevron. Los primeros se hacen de acuerdo con el perímetro exacto de la superficie, mientras que los segundos incluyen dos piezas que empatan una con la otra en forma de L y que igualan la superficie del perímetro. Al igual que los empaques FIP, los empaques troquelados a la medida, de una sola pieza, no tiene uniones. Sin embargo, normalmente éstos son más costosos.
Lo interesante es que cada una de estas alternativas ha sido sometida a diferentes pruebas de resistencia a fin de cumplir con las normas establecidas internacionalmente. Son, por ejemplo, expuestos al chorro de agua, inmersión en agua, de tensión y elongación, resistencia al frío, de compresión y un sistema de absorción de agua.
Lo anterior nos da mayor tranquilidad al saber que alguien más se ha tomado el tiempo de comprobar que el empaque que vamos a adquirir cumpla con las normas y estándares de calidad, que dicho sea de paso, existen cuatro organizaciones más reconocidas para estándares de gabinetes y son la Comisión Electrotécnica Internacional (IEC), la Asociación Nacional de Fabricantes Eléctricos (NEMA), la Asociación de Estándares Canadienses (CSA) y Underwriters Laboratories (UL).
Materiales de acuerdo con el ambiente
Otro factor que debemos tomar en cuenta al momento de seleccionar un empaque tiene que ver con el material con el que está hecho. La elección entre una u otra opción tiene que ver con el tipo de ambiente en donde se planean instalar. Lo anterior, debido a que cada uno ofrece diferentes rangos de temperatura y resistencias a la compresión, entre otras características. Los materiales más utilizados son los siguientes:
1. Poliuretano: Recomendado para ambientes que manejan rangos de temperatura de entre -40 a 70 °C; tiene buena resistencia de compresión y ofrece la facilidad para crear empaques de formas irregulares.
2. Neopreno: Se usa en la fabricación de empaques a la medida y en tiras, soporta rangos de temperatura de entre -55 a 120 °C, ofrece resistencia a químicos, abrasión y desgaste, además de que son a prueba de agua.
3. Nitrilo: Resistente a la compresión, al desgaste y abrasión, pero no muy tolerante al ozono, rayos UV y otros elementos relacionados con el clima. Su tolerancia a temperaturas va desde los -40 a 121 °C.
4. Silicón: Soporta temperaturas de entre -40 a 232 °C, alta resistencia a la compresión, ozono, rayos UV y otros elementos relacionados con el clima; es fabricado por molde o troquelados.
5. Viton: Utilizan material fluorelastómero que soporta temperaturas de entre -28 a 204 °C, además de que ofrece resistencia a químicos cáusticos.
Al tomar en cuenta estos pequeños detalles: material, medio ambiente al que serán expuestos y costos, la tarea de buscar el empaque que mejor se adecua a nuestras necesidades se vuelve más sencilla. Incluso, al seleccionar el que se ajusta a nuestras necesidades podemos estar tranquilos de que nuestros equipos tendrán un óptimo funcionamiento de los gabinetes, así como una vida más duradera.
__________________________
* Director de Operaciones para América Latina en PENTAIR-SOLUCIONES PARA LA PROTECCIÓN DE EQUIPOS